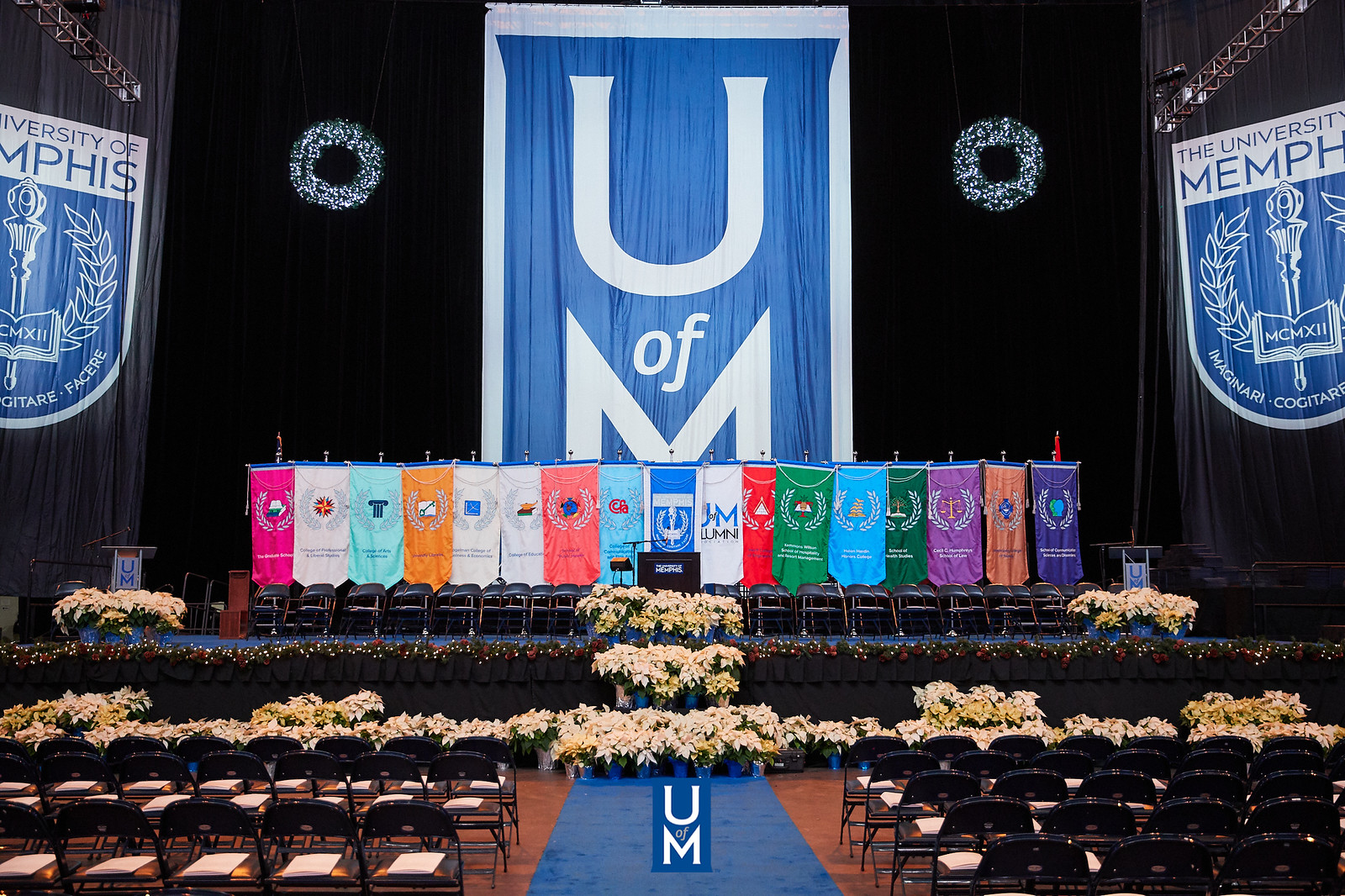
Electronic Theses and Dissertations
Date
2020
Document Type
Dissertation
Degree Name
Doctor of Philosophy
Department
Mechanical Engineering
Committee Chair
Ebrahim Asadi
Committee Member
Gladius Lewis
Committee Member
Amir Hadadzadeh
Committee Member
Ranganathan Gopalakrishnan
Abstract
Direct metal laser sintering (DMLS) is a widely used powder bed fusion (PBF) additive manufacturing (AM) technology that offers extensive capabilities to fabricate complex metallic components. In the DMLS process, part fabrication involves small moving melt-pools formed by the interaction of laser beam and metal powders. The formation of a melt-pool and subsequently its rapid solidification results in alteration of properties and microstructure of the product. Therefore, understanding and predicting relationships between DMLS process parameters and melt-pool characteristics is critical to control and improve the properties of parts. The melt-pool formation in this process is very similar to what occurs in metal laser welding, having solid metallic parts rather than metal powders, plus laser welding is more investigated and is better known compare to DMLS. So, a critical review of the literature on experimental and modeling studies on laser welding, with the focus being on the influence of process parameters on geometry, thermodynamics, fluid dynamics, microstructure, and porosity characteristics of the melt-pool is presented. However, the DMLS process has several variables, altering which increases the complexity of the correlations between them and the final properties. A solution is to isolate the variable sets from the other ones during the investigation. Therefore, keeping all the processing parameters constant, an investigation of the size and geometry dependence of the dimensional accuracy of the DMLS process is presented. For all features, with different geometries and different sizes, the percent error significantly increases with decreasing the feature size. Then, the effect of thickness, orientation, distance from free edges, and height on the mechanical properties and their correlations to material microstructure and thermal history as dictated by DMLS process parameters are investigated and the results are correlated to the porosity volume fraction and their elongation direction, prior grain width and orientation, nanoparticle volume fraction, martensitic decomposition to + and orthorhombic structure, and Oxygen content variation. Furthermore, the influence of five most influential DMLS processing parameters, i.e. laser power, scan speed, hatch spacing, layer thickness, and stripe width, on relative density, microhardness, and surface roughness are thoroughly investigated. Two design of experiment (DoE) methods, including the Taguchi and fractional factorial DoE for response surface method (RSM), along with an artificial neural network (ANN) are designed and trained to predict the response values. A multi-objective RSM model is developed for the optimization of DMLS processing parameters. It is shown that the proposed ANN model can most accurately predict various response properties of DMLS components.
Library Comment
Dissertation or thesis originally submitted to ProQuest
Recommended Citation
Fotovvati, Behzad, "DIRECT METAL LASER SINTERING OF TI-6AL-4V ALLOY: PROCESS-PROPERTY-GEOMETRY EMPIRICAL MODELING AND OPTIMIZATION" (2020). Electronic Theses and Dissertations. 2545.
https://digitalcommons.memphis.edu/etd/2545
Comments
Data is provided by the student.