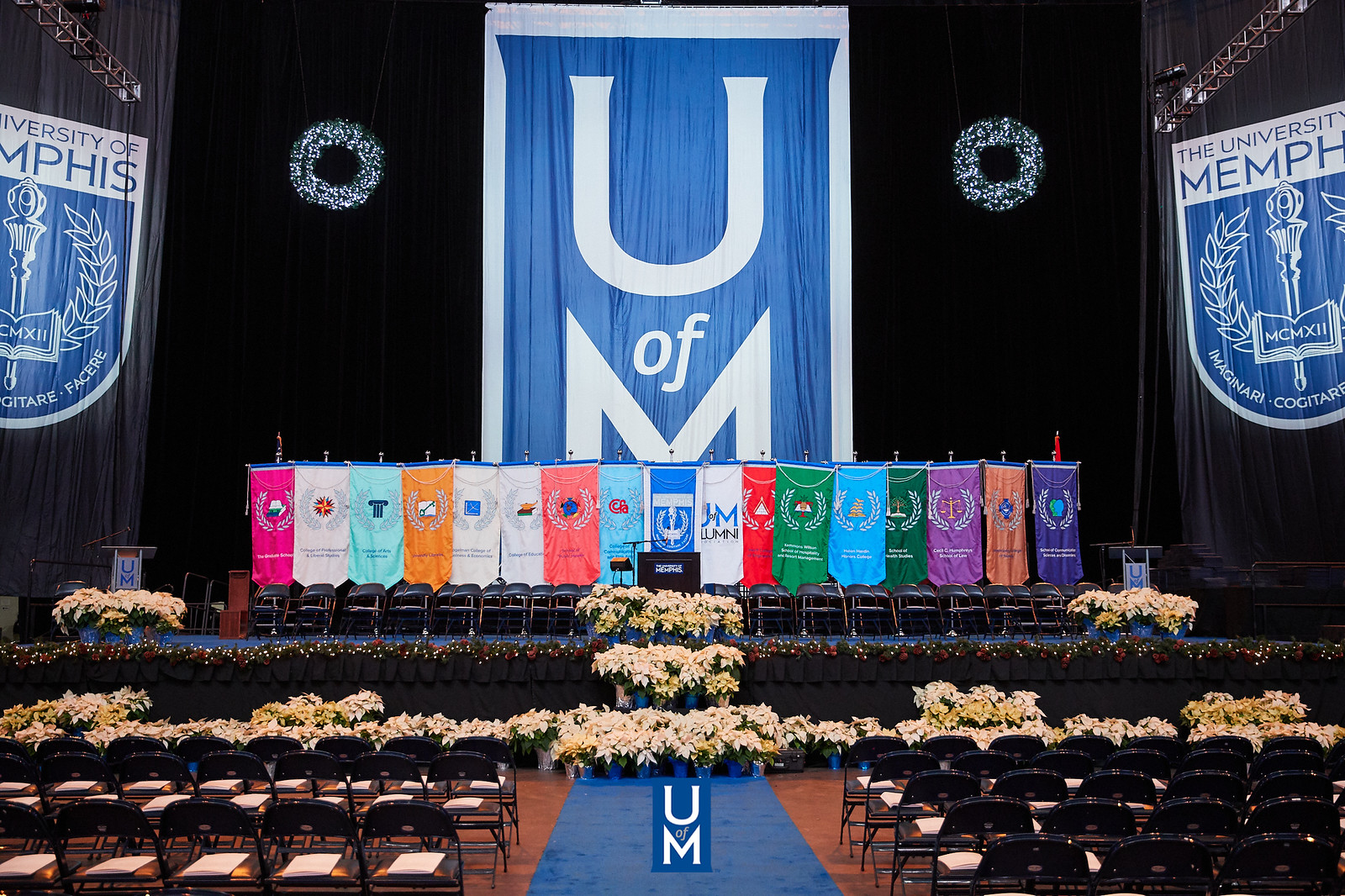
Electronic Theses and Dissertations
Date
2019
Document Type
Dissertation
Degree Name
Doctor of Philosophy
Department
Mechanical Engineering
Committee Chair
Ali Fatemi
Committee Member
Amir Hadadzadeh
Committee Member
Ebrahim Asadi
Committee Member
Gladius Lewis
Abstract
Additive manufacturing (AM) technology has gained significant attention in recent years due to several important advantages. However, design of critical load carrying parts using this technique is still at its infancy, partly due to the inferior performance and lack of sufficient understanding of fatigue behavior of AM metals as compared to their wrought counterparts. Similar to most other components in different industries, AM parts typically undergo cyclic loadings through their service life, therefore, fatigue performance is a key performance criterion. In addition, biaxial and multiaxial stresses are common for many components, even under nominal uniaxial loading conditions where the stress state can be multiaxial due to the complexities in the geometry such as notches, or presence of multidirectional residual stresses. Such effects are more pronounced in AM, where geometry complexities result in stress concentrations, multidirectional residual stresses from the fabrication process are inevitable, and produced defects are typically directional resulting in anisotropy. Despite this fact, previous works have only focused on constant amplitude uniaxial fatigue evaluation of AM materials. One of the main advantages of the AM technique is the capability in fabricating complex geometries, in which, as mentioned, stress concentrations might be inevitable. In addition, the rough surface and un-melted particle clusters on the surface of the AM fabricated parts can also act as stress concentrations and significantly affect the fatigue behavior. Therefore, it is essential to be able to accurately characterize and predict the materials behavior in the presence of stress concentrations, such as notches. Regarding to the loading history, service load histories are typically variable amplitude in nature, where the applied stress states may vary with time and, hence, load sequence and their interactions could play an important role in such loadings. This may become more complicated for AM when considering the effect of defects, both internal and surface, and their interaction with the stress concentrations caused by the notches. The effect of such loading for AM metals and processes in terms of cumulative fatigue damage evolution need to be considered, particularly when the stress states are multiaxial. The main objective of this study was to investigate the cyclic and fatigue behaviors of AM metallic alloys under constant and variable amplitude axial, torsion, and combined axial-torsion loadings. This included both unnotched and notched conditions. Two widely used metallic materials in AM were considered for this study. These include Ti-6Al-4V and 17-4 PH stainless steel alloys. Ti-6Al-4V is a high strength, light weight, and high corrosion resistant material with many applications in aerospace and biomedical industries, and 17-4 PH is a Precipitated Hardened (PH) stainless steel with common applications in corrosion resistant applications such as aerospace, petroleum, and chemical industries. The two materials were chosen to get an understanding of the general applicability of the findings for AM metals. Depending on the material, effect of different post-fabrication treatments such as stress relieving and Hot Isostatic Pressing (HIP) methods were evaluated. Surface finish effect was also considered as another key consideration in mechanical behavior evaluation of the AM alloys. To evaluate the build orientation effect, monotonic and fatigue performance of the vertically and diagonally built (at 45) specimens were compared. All of the results from the AM metals were also compared to the fatigue behavior of their conventional wrought metals. Since response of the materials under cyclic loading can vastly differ from their monotonic response due to phenomenon such as cyclic softening or cyclic hardening, both monotonic and cyclic deformation behaviors were studied. Proper fatigue analysis where plastic deformation is present requires characterization of the cyclic deformation behavior. Failure mechanism(s) and cracking behaviors were also carefully examined for all of the materials with different conditions. Knowing these behaviors under cyclic loading is essential to performing accurate fatigue analysis. For the analysis, based on the experimental results, observed microstructures and defect structures, failure mechanisms, and cracking behaviors of the materials with different post treatment conditions, appropriate predictive multiaxial fatigue life prediction models were applied. These include classical equivalent stress- and strain- based analysis approaches as well as more advanced analysis techniques such as critical plane-based damage parameters. For the notched specimen tests, different models, including computational, analytical and empirical approaches were discussed to estimate the local stresses/strains and predict the fatigue lives. However, due to the presence of internal defects in AM materials and their interactions with notches, some of these methods may not be appropriate for AM metals. Therefore, a modification to the Theory of Critical Distance (TCD) was proposed to account for the presence of internal defects in AM metals. In order to evaluate life prediction procedures under variable amplitude multiaxial loading conditions, different aspects were considered to predict the fatigue life. These include studying the effect of defects (both internal and surface), anisotropy, and residual stresses, which may result in different load sequence effects and, therefore, different fatigue life predictions as compared to the conventionally fabricated metals.Using the geometrical freedom offered by additive manufacturing, some novel specimens geometries were also proposed. These included a plate-type specimen geometry for axial fatigue testing, a hollow cylindrical specimen for torsion testing, and two thin-walled circular cross section specimens for torsion or axial-torsion fatigue testing. The proposed geometries reduce the stress concentration at the gage-to-grip transition area, improve the uniformity of the shear stress distribution throughout the wall thickness, and increase buckling resistance during the compression part of the loading cycle.
Library Comment
Dissertation or thesis originally submitted to ProQuest
Recommended Citation
Molaei, Reza, "Multiaxial Fatigue Behavior of Additive Manufactured Metals: Experiments and Modeling" (2019). Electronic Theses and Dissertations. 2681.
https://digitalcommons.memphis.edu/etd/2681
Comments
Data is provided by the student.