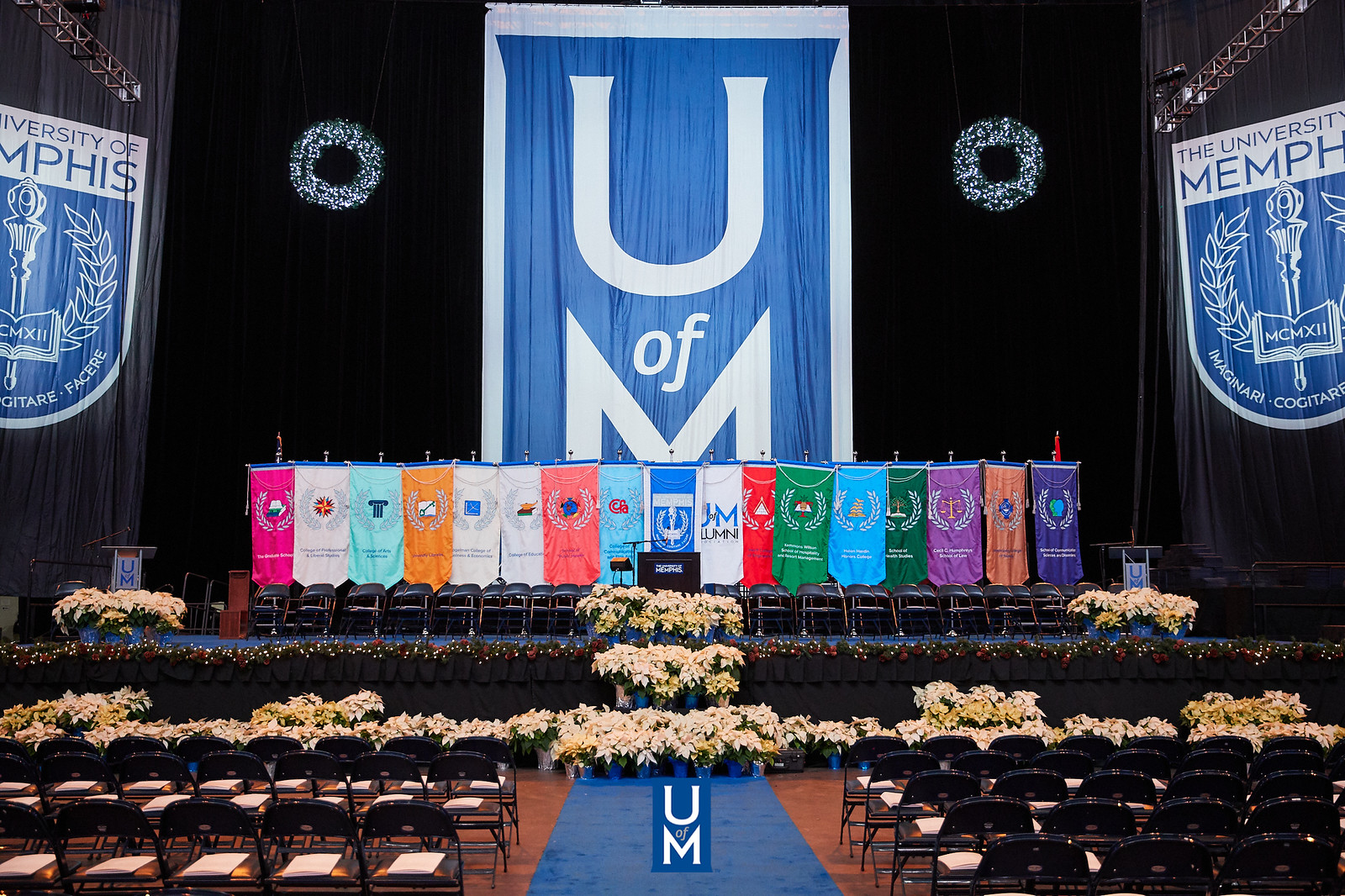
Electronic Theses and Dissertations
Date
2022
Document Type
Dissertation
Degree Name
Doctor of Philosophy
Department
Mechanical Engineering
Committee Chair
Ebrahim Asadi
Committee Member
Reza Molaei
Committee Member
Amir Hadadzadeh
Committee Member
Gladius Lewis
Committee Member
Danijela Rostohar
Abstract
Laser-powder bed fusion (L-PBF) is a metal additive manufacturing (MAM) method that promises the ability to make geometrically complex parts not previously attainable through conventional manufacturing methods. This method involves spreading a thin layer of powdered metal over a metal build plate and then, using a laser beam to fuse a desired cross-section. After that, the build plate is lowered, another layer of powder is spread over the top, forming the powder bed, and the laser beam is fired again to fuse the next desired cross-section. By repeating this sequence, the desired geometry is manufactured out of the powder bed. This process is prone to various errors, which result in defects being formed inside the parts. For example, it is common for the density of the powder bed to vary along the length of the build plate, possibly resulting in a performance gap between two parts manufactured at the same time. Therefore, understanding the processes involved in powder bed formation, how L-PBF variables affect powder bed properties, and how these properties, in turn, affect the properties of the manufactured parts are critical to improving L-PBF. The first part of this work involved determination of powder bed density at various locations along the build plate (“part manufacturing location”), detailed characterization of subsurface defects in the part as a function of part manufacturing location, and determination of the uniaxial fatigue performance of the part as a function of part manufacturing location. It was found that part manufacturing location had a marginal effect on the powder bed density, a significant effect on subsurface defect characteristics, and only a marginal effect on uniaxial fatigue performance. To improve the quality of LPBF-manufactured parts post-processing operations, such as heat treatments, hot isostatic pressing, and media blasting, are often used. One post-processing method that, to date, has not commonly been applied to these parts is laser shock peening (LSP). This technique involves subjecting a part to a high-energy short-pulse laser beam and generating a plasma shock wave on its surface. This shock wave is then confined by a water jacket and forced downward through the part. As the shock wave dissipates, it induces a field of compressive residual stress in the near-surface region of the part, which helps to improve its mechanical performance. Because the laser beam is computer-controlled, the extent of the compressive residual stress zone in a part can be precisely adjusted even in parts with complex geometry, making LSP particularly attractive for application in MAM. The second part of this work quantified the effect of LSP on the distribution of compressive residual stress in the near- surface zones on vertically manufactured parts, the effect of LSP on near-surface defects in these parts, the effect of LSP on four-point bending fatigue performance of parts with an as-built surface finish, and the effect of LSP on uniaxial fatigue performance of parts with a machined surface finish. It was found that LSP had a significant effect on the compressive residual stress in the near-surface zone, a significant effect on characteristics of near-surface defects, significantly enhanced four-point bending fatigue performance, while only marginally affecting the uniaxial fatigue performance. As all L-PBF parts are made by stacking flat layers on top of one another, a smooth curve cannot be made. This results in small steps being left on the surface of the part. The third part of this work determined the effect of LSP on the near-surface compressive residual stress distribution and four-point bending fatigue characteristics of parts manufactured at an angle of ±40o relative to the vertical axis (which simulated steps on a part). It was found that while the compressive residual stress distribution was not significantly affected by manufacturing orientation, and LSP had a significantly positive effect on the fatigue performance regardless of manufacturing orientation.
Library Comment
Dissertation or thesis originally submitted to ProQuest
Notes
Embargoed until 11/3/2024
Recommended Citation
Fitzmire, Michael, "Investigation of Improvement of Ti-6Al-4V Parts Made Through Laser Powder Bed Fusion Using In-Situ Monitoring of the Powder Bed Formation and the Application of Laser Shock Peening" (2022). Electronic Theses and Dissertations. 3177.
https://digitalcommons.memphis.edu/etd/3177
Comments
Data is provided by the student.