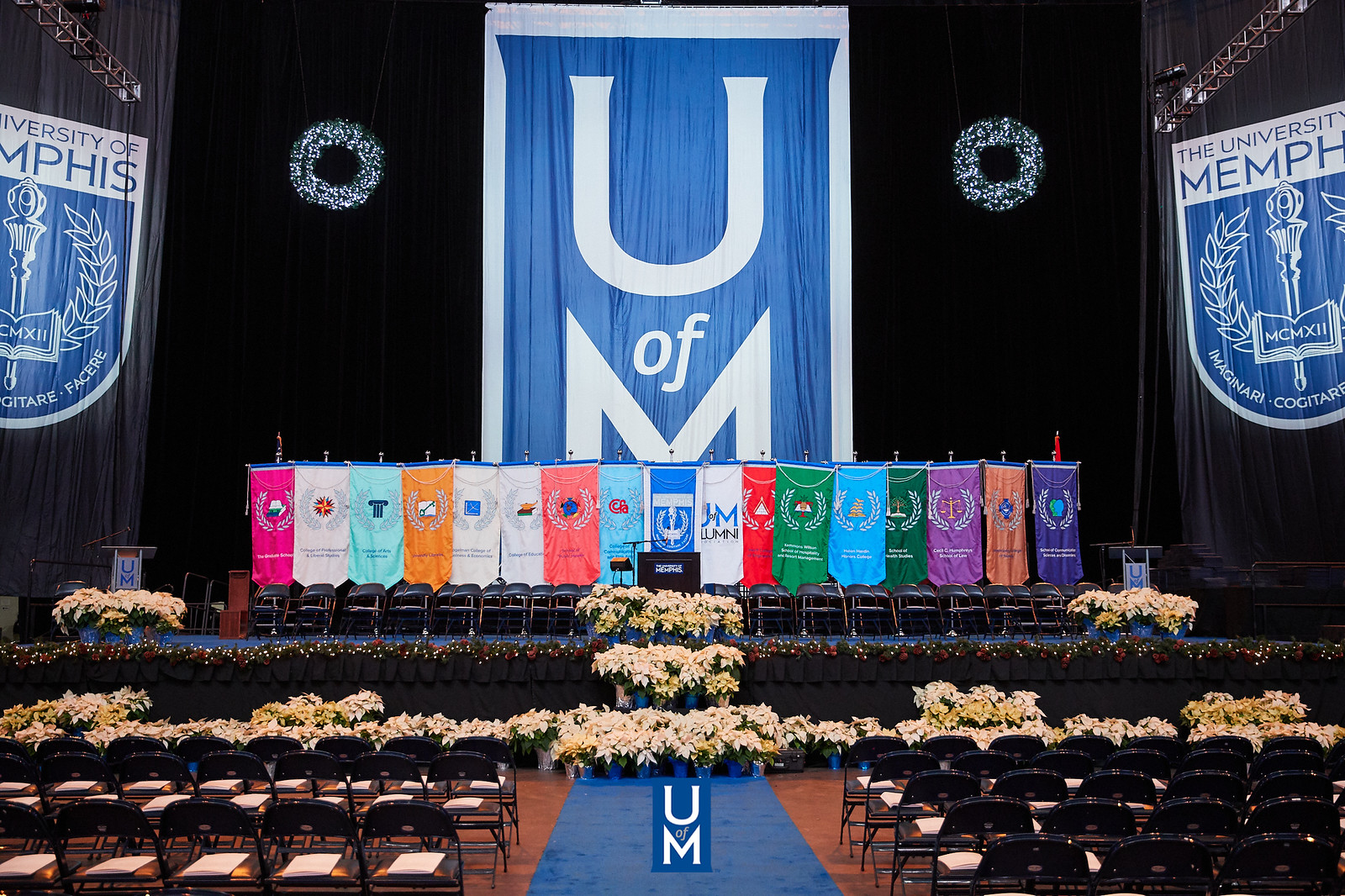
Electronic Theses and Dissertations
Date
2023
Document Type
Dissertation
Degree Name
Doctor of Philosophy
Department
Mechanical Engineering
Committee Chair
Ali Fatemi
Committee Member
Gladius Lewis
Committee Member
Amir Hadadzadeh
Committee Member
John Williams
Committee Member
James C. Newman
Committee Member
Jr.
Abstract
Additive manufacturing, such as laser powder bed fusion (L-PBF), offers several advantages over conventional manufacturing processes, such as forging, notably increased geometric freedom in designs, economical production of small lots of parts, and on-site fabrication of replacement parts. However, due to the unique thermal history of additively manufactured parts, there are larger variations in microstructure, defects, and residual stresses than are observed in conventionally manufactured parts. Additionally, although post-processing treatments can often improve mechanical properties of additively manufactured parts, there is an associated cost of these treatments with each which may negate some of the key advantages of using additive manufacturing over conventional processes. For conventionally manufactured metals, which tend to have consistent defect content and microstructure, crack initiation approaches have been shown to result in adequate predictions of fatigue life. However, for additively manufactured metals, in which local defect and microstructural features may vary depending on a multitude of factors, such as the selected process parameters, part geometry, part orientation (with respect to the build plate), and part location on the build plate, crack initiation approaches to fatigue life prediction are not reliable. The goal of this work is to explicitly model defects as small cracks and use linear elastic fracture mechanics to predict the mixed-mode growth of small cracks in additively manufactured metals. First, a novel method is proposed to determine the uniaxial equivalent stress amplitude for multiaxial loading conditions using the critical plane concept. Then, mixed-mode small crack growth behavior of two L-PBF manufactured metals is characterized. Mixed-mode small crack growth rates are modelled using a critical plane-based stress intensity factor range, and the Hartman-Schijve crack growth equation is used to represent mixed-mode small crack growth rates for a variety of loading conditions. A novel method is presented for converting Mode I crack growth properties into their equivalent mixed-mode properties. Lastly, a framework for the prediction of mixed-mode small crack growth rates and direction under multiaxial variable amplitude loading histories is then proposed. Comparisons of predictions with experimental results show that the proposed framework results in good predictions of mixed-mode small crack growth rate and direction in additively manufactured metals.
Library Comment
Dissertation or thesis originally submitted to ProQuest.
Notes
Embargoed until 2025-11-21
Recommended Citation
Markham, Matthew Jordan, "Mixed-Mode Small Crack Growth in Additively Manufactured Metals" (2023). Electronic Theses and Dissertations. 3315.
https://digitalcommons.memphis.edu/etd/3315
Comments
Data is provided by the student.