Breaking strength-ductility trade-off in laser-powder bed fused Fe–Cr–Ni–Al maraging stainless steel: Controlled precipitation and preserved dislocations
Abstract
In the current study, cylindrical rods of Fe–Cr–Ni–Al maraging steel (with the brand name CX) are fabricated using the laser-powder bed fusion (L-PBF) technique. The material is analyzed using the differential scanning calorimetry (DSC) technique under continuous heating at different heating rates. The DSC results are employed to identify the heat flow peaks associated with the precipitation and austenite reversion phase transformations. The peaks are then analyzed and processed to determine the onset, peak, and end temperatures associated with each phase transformation. These results are used to calculate the degree of phase transformation under non-isothermal conditions and to evaluate the activation energy of transformation through the Kissinger method. In the next step, the modified Johnson-Mehl-Avrami-Kolmogorov (JMAK) model is employed to model the kinetics of phase transformations during non-isothermal heating. The validated model is then used to predict the kinetics of precipitation and austenite reversion phase transformations under isothermal aging heat treatments. The isothermal modeling results are employed to design a direct aging heat treatment to promote the evolution of nanometric β-NiAl precipitates and meanwhile preserve the pre-existing dislocation networks. Such a heat treatment results in the enhancement of both yield and tensile strengths from 929 MPa and 1032 MPa in the as-built condition to 1659 MPa and 1738 MPa after heat treatment. Meanwhile, ductility slightly changes from 15.3% in the as-built condition to 14.7% after heat treatment. Such an achievement in breaking the strength-ductility trade-off is due to a controlled heat treatment process that preserves the dislocation networks.
Publication Title
Materials Science and Engineering: A
Recommended Citation
Fabian, R., & Hadadzadeh, A. (2023). Breaking strength-ductility trade-off in laser-powder bed fused Fe–Cr–Ni–Al maraging stainless steel: Controlled precipitation and preserved dislocations. Materials Science and Engineering: A, 868 https://doi.org/10.1016/j.msea.2023.144761
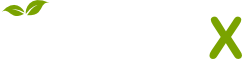
- Citations
- Citation Indexes: 8
- Usage
- Abstract Views: 1
- Captures
- Readers: 7
- Mentions
- News Mentions: 1