Study of direct aging heat treatment of additively manufactured PH13–8Mo stainless steel: role of the manufacturing process, phase transformation kinetics, and microstructure evolution
Abstract
Direct aging heat treatment recipes were developed for additively manufactured (AM) PH13–8Mo stainless steel by studying the kinetics of precipitation phase transformation in the as-built material. The samples were printed using two AM processes; i.e., arc-directed energy deposition (arc-DED) and laser-powder bed fusion (L-PBF) techniques. The as-built samples were characterized using differential scanning calorimetry (DSC) to determine the characteristics of precipitation phase transformation. Due to different thermal histories during the arc-DED and L-PBF processes, the resulting microstructures and physical properties were different; therefore, the precipitation kinetics were different. The kinetics results were used to design a direct aging heat treatment to promote the formation of β-NiAl precipitates. Two different heat treatment recipes were designed considering the differences between the two materials. Direct aging of arc-DED-PH13-8Mo resulted in a concurrent improvement in strength and ductility, while direct aging of L-PBF-PH13-8Mo resulted in a significant increase in strength and retention of ductility. The microstructure was then correlated to the physical (i.e., the kinetics of precipitation) and mechanical (i.e., strength and ductility) properties. Concurrent strength and ductility improvement in the arc-DED-PH13-8Mo was controlled by the evolution of nano-scaled β-NiAl clusters. In the L-PBF-PH13-8Mo, the strength enhancement was governed by the evolution of nano-scaled β-NiAl precipitates, while the ductility retention was dictated by preserving the pre-existing dislocation networks.
Publication Title
Journal of Materials Research and Technology
Recommended Citation
Moniruzzaman, F., Shakil, S., Shaha, S., Kacher, J., Nasiri, A., Haghshenas, M., & Hadadzadeh, A. (2023). Study of direct aging heat treatment of additively manufactured PH13–8Mo stainless steel: role of the manufacturing process, phase transformation kinetics, and microstructure evolution. Journal of Materials Research and Technology, 24, 3772-3787. https://doi.org/10.1016/j.jmrt.2023.04.023
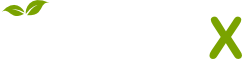
- Citations
- Citation Indexes: 15
- Usage
- Abstract Views: 8
- Captures
- Readers: 8
- Mentions
- News Mentions: 1